Process Scale-Up Manufacturing: Going from Good to Outstanding
While it's true that following a baking recipe on your own can yield satisfactory results, the outcome often needs more finesse and nuanced understanding that comes with experience.
On the other hand, having a master chef working alongside you transforms the process into a rich learning experience. Their insights, tips, and years of acquiring expertise elevate the outcome, yielding the possibility of achieving exceptional, elusive results.
Collaboration not only enhances the final product. It also deepens your understanding of the craft, leaving you better equipped for future endeavors. This “in-the-kitchen-with-you” baking analogy paints a reasonably accurate picture of what biopharma developers can expect when they engage in the process scale-up manufacturing services Ascendia offers.
Understanding Process Scale-Up Manufacturing
Transitioning from small-scale laboratory formulations to large-scale manufacturing is critical in pharmaceutical development. This process demands meticulous attention to detail, world-class expertise, and technological prowess.
Ascendia, a leader in pharmaceutical development services, stands uniquely positioned to navigate and excel in this arena. We offer high-end equipment and decades of proven outcomes to bolster confidence and drive success in drug formulation and development projects.
Appreciating the Complexity of Scale-Up Manufacturing
Scale-up manufacturing presents many challenges, particularly when transitioning from initial batch formulations to more extensive production lines. Technicians must finely tune the parameters to ensure alignment with larger batches, optimizing process conditions and mitigating risks of batch failure, hence, saving time and cost. The meticulous attention to detail required underscores the challenges of scaling formulations effectively.
This ongoing supervision makes having a "master chef" working alongside so critical. Experience and access to the latest technologies make all the difference in achieving quality results within a predetermined timeline and expectation.
Overcoming the More Common Stumbling Blocks
During Phase One of biopharmaceutical development, developers typically face several challenges when moving into process scale-up manufacturing. Some of the more common challenges include:
- Process Optimization: Transitioning from small-scale laboratory processes to larger-scale manufacturing requires optimization of various parameters such as -processing conditions, mixing times, and temperature profiles. Ensuring the optimized process is scalable — without compromising product quality or yield — nearly always presents a significant challenge.
- Equipment Compatibility: The equipment used for small-scale production may not be directly transferrable to large-scale manufacturing due to differences in scale, material compatibility, and operating conditions. Adapting or acquiring new equipment that meets regulatory standards and process requirements can be a logistical and financial challenge.
- Quality Control and Assurance: Maintaining consistent product quality and compliance with regulatory standards is paramount during scale-up manufacturing. Developers must establish robust quality control measures and analytical methods to monitor critical process parameters and product attributes throughout the scale-up process.
- Resource Allocation: Scale-up manufacturing requires significant resource investments, including raw materials, equipment, personnel, and facilities with robust compliances. The effective allocation of resources while managing costs and timelines presents a challenge for biopharma developers. Informed decision-making is particularly critical during early-stage development when funding and resources may be limited.
- Regulatory Compliance: Compliance with regulatory requirements and guidelines is essential at every stage of the drug development process, including scale-up cGMP manufacturing. Developers must navigate complex regulatory frameworks and adhere to current Good Manufacturing Practices (cGMP) to ensure product safety, efficacy, and quality throughout the scale-up process.
- Risk Management: Scale-up manufacturing introduces inherent risks, including batch variability, equipment failures, and process deviations, which can impact product quality, product failure and patient safety. Implementing comprehensive, time-tested risk management strategies and contingency plans is essential to mitigate these risks and ensure smooth scale-up operations.
- Technology Transfer: Collaborating with contract drug manufacturing organizations (CDMOs) or transitioning manufacturing processes between facilities through technology transfer ensures seamless transfer of knowledge, expertise, and process parameters while maintaining consistency and integrity - - for successful scale-up and manufacturing.
Addressing these challenges requires careful planning, collaboration, and expertise to effectively navigate the complexities of process scale-up and manufacturing. Biopharma developers must leverage scientific insights, technological innovations, and regulatory knowledge to overcome these challenges and advance their drug candidates toward commercialization.
Ascendia's Unique Value Proposition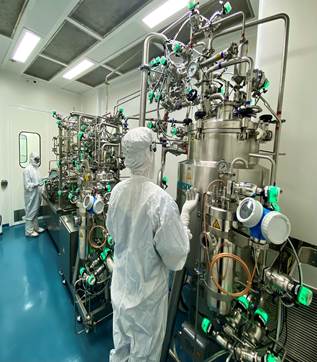
What sets Ascendia apart from its competitors lies in its comprehensive approach to process scale-up and manufacturing. The team at Ascendia consistently emphasizes the importance of expertise, technology, and know-how in navigating these challenges.
Ascendia has the capabilities with deep understanding of the nuances of scaling formulations effectively. Identifying and swiftly addressing problems is an ongoing testament to Ascendia's commitment to excellence.
The Role of Technology and Expertise
Ascendia's competitive edge is evident in its robust technological infrastructure and seasoned team of experts. With a keen understanding of formulation challenges and manufacturing intricacies, Ascendia integrates technology seamlessly into the scale-up process, leading to robust manufacturing outcomes.
By leveraging advanced technologies and industry insights, Ascendia optimizes formulations with manufacturing in mind, ensuring a streamlined and efficient transition from development to production.
The Ascendia Advantages: Time, Knowledge, and Efficiency
Central to Ascendia's process scale-up philosophy is recognizing time as a critical asset in pharmaceutical development. Our team consistently underscores the significance of saved time and leverages the benefits of Ascendia's end-to-end manufacturing approach.
From pre-formulation through manufacturing, Ascendia's focus on the entire process streamlines operations, saves costs, and accelerates time to market — a logical outcome of its commitment to clients’ successes.
Begin the Conversation: Reach Out to Ascendia Today
In the dynamic landscape of pharmaceutical development, the difference between success and mediocrity often lies in the choice of partners and mutual commitments.
In the journey from formulation to manufacturing, Ascendia isn't just following a cookbook recipe—it's orchestrating a symphony of innovation and expertise, ensuring that every project reaches its full potential.
Ascendia's unwavering commitment to excellence, unmatched expertise, and technological prowess make it the premier choice for process scale-up and manufacturing. Contact Ascendia today to discover how their tailored solutions can advance your drug -formulation and development projects to new heights of success, and expedite to market.